When it comes to choosing the right material for your next project, the debate of polyester resin vs epoxy resin is front and center.
Whether you’re building a boat, crafting jewelry, or repairing a surfboard, the resin you pick will shape your results—literally and figuratively.
In this deep dive, we’ll break down the real-world differences, bust some myths, and share insights you won’t find anywhere else. By the end, you’ll know exactly which resin is right for your project and why.
Key Takeaways
- Polyester resin is cost-effective and cures quickly, but it’s less durable and has more fumes.
- Epoxy resin offers superior strength, adhesion, and versatility, but at a higher price point.
- Your choice should depend on your project’s requirements: budget, durability, appearance, and safety.
- We’ll also cover maintenance, environmental impact, and real-life user tips most guides skip.
- Key Takeaways
- What Are Polyester Resin and Epoxy Resin?
- Polyester Resin vs Epoxy Resin: Head-to-Head Comparison
- When Should You Use Polyester Resin?
- When Should You Use Epoxy Resin?
- Maintenance and Longevity
- Application Tips and Tricks
- Common Myths About Polyester and Epoxy Resins
- Real-World Scenarios: Which Resin Wins?
- Polyester Resin vs Epoxy Resin in Boat Construction
- Personal Experience with Polyester Resin
- Final Thoughts
What Are Polyester Resin and Epoxy Resin?
Let’s start with the basics. Both polyester and epoxy resins are synthetic polymers that harden (or “cure”) into tough, solid plastics. They’re used in a wide range of industries, from construction and automotive to art and crafts. But despite their similar uses, their chemical makeup and performance are quite different.
- Polyester resin is created by reacting dibasic organic acids and polyhydric alcohols. It’s the most widely used resin globally, especially in fiberglass applications.
- Epoxy resin is made by reacting epichlorohydrin with bisphenol-A, resulting in a two-part system (resin and hardener) that must be mixed before use.
Polyester Resin vs Epoxy Resin: Head-to-Head Comparison
1. Cost and Accessibility
Polyester resin wins hands-down when it comes to price. It’s typically 30-50% cheaper than epoxy for the same volume, making it a go-to for large projects or when budget is tight. This is why you’ll find it in boats, car bodies, and large molds—where covering lots of surface area matters (Resiners Guide).
Epoxy resin is more expensive, but you get what you pay for: better strength, adhesion, and clarity.
2. Strength and Durability
- Epoxy resin is the clear winner in terms of strength, flexibility, and resistance to impact, chemicals, and water. It’s less likely to crack or become brittle over time.
- Polyester resin is more rigid and can be brittle, especially under stress or with age. It’s suitable for structural parts when cost trumps longevity.
3. Adhesion and Bonding
- Epoxy resin bonds exceptionally well to a wide range of materials—wood, metal, concrete, and even old cured epoxy. This makes it ideal for repairs and composite builds.
- Polyester resin does not stick as well, especially to wood and metals. It’s best paired with fiberglass mat or cloth for structural strength (Resin Expert).
4. Curing Time and Working Window
- Polyester resin cures quickly—sometimes within 30 minutes. This is great for production speed but leaves little time for adjustments.
- Epoxy resin has a longer “pot life” (working time), giving you more flexibility for complex projects or detailed work.
5. Appearance and Clarity
- Epoxy resin cures crystal clear and is highly UV resistant (with the right additives). It’s perfect for art, jewelry, and surfaces where aesthetics matter.
- Polyester resin can yellow over time and is more prone to developing a cloudy finish. It’s less ideal for clear casting or decorative surfaces.
6. Fumes and Safety
- Polyester resin emits strong, often unpleasant fumes (styrene), which require good ventilation and protective gear.
- Epoxy resin is much less smelly, but you should still wear gloves and a mask, as skin contact can cause allergic reactions.
7. Environmental Impact
Here’s where most guides stop short—but it’s important! Polyester resin is petroleum-based and releases VOCs (volatile organic compounds) during curing, which can harm indoor air quality and the environment.
Epoxy is also petroleum-based but generally releases fewer VOCs, especially newer “eco” formulas.
8. Shelf Life and Storage
- Epoxy resin has a longer shelf life and is less sensitive to moisture during storage.
- Polyester resin can degrade faster, especially if exposed to humidity or not sealed properly.
When Should You Use Polyester Resin?
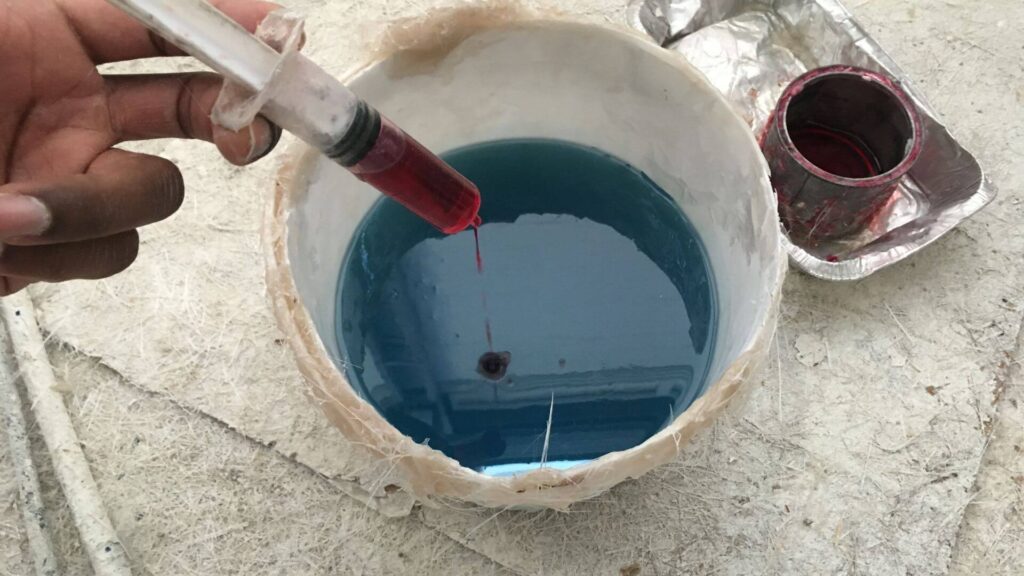
Best Uses
- Large fiberglass projects: Boats, car bodies, pools, and tanks.
- Budget builds: When cost is the main concern.
- Quick fixes: Where speed matters more than aesthetics or long-term durability.
What to Watch Out For
- Poor adhesion: Don’t use polyester resin to glue wood or metal.
- Fumes: Always work in a well-ventilated area.
- Yellowing: Not ideal for items that require a clear or glossy finish.
When Should You Use Epoxy Resin?
Best Uses
- High-strength bonding: Woodworking, surfboards, repairs, and laminating.
- Crystal-clear casting: Jewelry, river tables, art, and bar tops.
- Waterproofing: Perfect for sealing and protecting surfaces exposed to moisture.
What to Watch Out For
- Higher cost: Factor this into your project budget.
- Mixing accuracy: Epoxy requires precise measurement and mixing for best results.
- Allergies: Wear gloves and avoid skin contact.
Maintenance and Longevity
How Do Projects Hold Up Over Time?
Epoxy resin projects tend to age gracefully. With its superior moisture resistance, UV light (when UV inhibitors are added), and physical stress, epoxy is the go-to for heirloom-quality crafts, outdoor furniture, and marine applications. If you’re making something you want to last for decades, epoxy is your friend.
Polyester resin, on the other hand, can become brittle and yellow with prolonged UV exposure, especially if left unpainted or uncoated. For outdoor or high-wear projects, regular maintenance—like sanding, recoating, or painting—may be necessary to keep things looking and performing their best.
Application Tips and Tricks
Getting the Best Results with Polyester Resin
- Catalyst matters: Always measure your hardener (usually MEKP) carefully. Too much or too little can cause weak spots or incomplete curing.
- Temperature control: Work in a well-ventilated, temperature-controlled space. Ideal curing temperatures are typically between 70–80°F (21–27°C).
- Layering: For thick builds, work in layers to avoid heat buildup and cracking.
Getting the Best Results with Epoxy Resin
- Mix thoroughly: Scrape the sides and bottom of your mixing cup to ensure all the resin and hardener are fully combined.
- Bubble control: Use a heat gun or torch to pop surface bubbles right after pouring.
- Color and additives: Epoxy takes pigments, metallic powders, and even glow-in-the-dark additives beautifully—just make sure any additions are compatible.
Common Myths About Polyester and Epoxy Resins
Myth #1: “Epoxy is always better.”
Not necessarily! Epoxy is stronger and more versatile, but it’s not always the best fit for every project. For large, non-structural builds where cost is king, polyester may be the smarter choice.
Myth #2: “You can use them interchangeably.”
This is a recipe for disaster. Each resin has unique chemical properties, and using the wrong one can mean poor adhesion, weak bonds, or even total project failure.
Myth #3: “All resins are equally toxic.”
While both resins require safety precautions, polyester’s fumes are much more hazardous in enclosed spaces. Epoxy can cause skin allergies, so always wear gloves, but its fumes are less intense.
Real-World Scenarios: Which Resin Wins?
Scenario 1: Building a Backyard Pond
You need a waterproof barrier that will last for years. Epoxy resin is the clear winner here—it bonds tightly to concrete, resists algae, and won’t degrade in sunlight (with a UV topcoat).
Scenario 2: Making a Surfboard
Most commercial surfboards use polyester resin because it’s cheap and works well with fiberglass. But many high-end custom boards now use epoxy for better flex and durability.
Scenario 3: DIY River Table
For that glass-like finish and depth, epoxy resin is unbeatable. Polyester will yellow and crack over time, ruining the effect.
Polyester Resin vs Epoxy Resin in Boat Construction
Polyester and epoxy resins have distinct roles in fiberglass boat building as well.
Polyester resin has been the go-to construction resin for decades. However, epoxies are becoming more popular for structural fabrication and critical connections.
A. Polyester Resin
- The low cost makes the polyester standard for fiberglass production
- Easy to work with in layup and spraying
- Requires more layers for adequate strength
B. Epoxy Resin
- Enhances laminate strength with fewer layers
- Specialty applications like hull/deck bonds, bulkheads
- Significantly higher material cost limit broad use
Epoxy resin’s exceptional bonding and moisture resistance confer major advantages where strength requirements are high. But budget-friendly polyester remains the resin used for most fiberglass boat production.
Personal Experience with Polyester Resin
Having worked with fiberglass and polyester resins building boats at Karnic Powerboats, I highly recommend polyester for boat construction.
During my time at Karnic, we used orthophthalic and isophthalic polyester resins to fabricate high-performance hulls and decks. I found polyester ideal for laminating multiple sheets of fiberglass mat, roving, and core materials.
The polyester resin is impregnated easily into glass fabrics during rolling and spraying. It cured smoothly into a rigid structure. With proper catalyst ratios and high-quality gel coats, we achieved glossy, durable exterior surfaces resistant to weathering.
While epoxy resins offer higher strength, polyesters deliver an unbeatable balance of workability and cost-effectiveness. Extra fiberglass layers offset lower strength. And with routine maintenance, polyester boats last for decades.
Given my positive experiences with polyester resins building boats at Karnic, I would certainly choose these dependable, easy-to-use resins again for fiberglass boat construction projects. They deliver excellent performance at a reasonable price point.
Final Thoughts
When it comes to the polyester resin vs epoxy resin debate, there’s no one-size-fits-all answer.
Consider your project’s purpose, budget, desired finish, and safety needs. For most high-performance or visually stunning projects, epoxy resin is worth the investment. For large, budget-conscious builds where speed matters, polyester resin still has its place.
If you’re new to resins, start small. Test both types on scrap material, see how they react, and get a feel for their quirks and strengths.
Don’t be afraid to experiment—some of the best innovations in resin art and construction come from makers who push the boundaries.
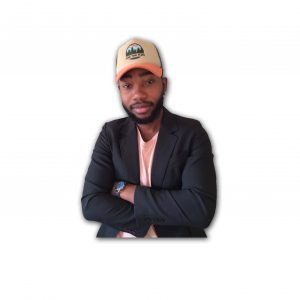
Founder of BoatGenesis, Warren has hands-on experience in fiberglass boat repairs, marine equipment testing, and powerboat building. Learn more about Warren.